AI Platform
for Combustion
Get A Free Demo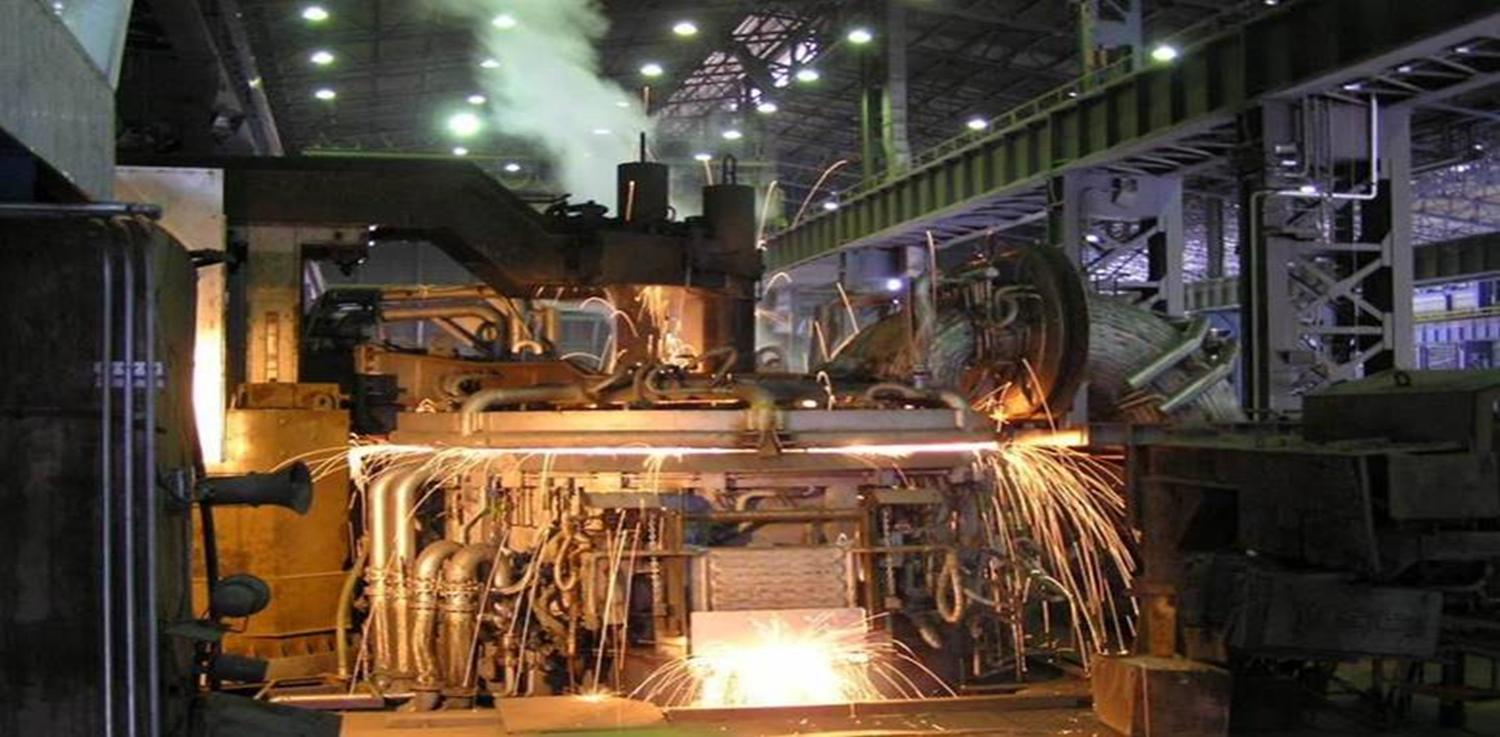

Why Choose Pyretek?
Our platform delivers measurable benefits across key operational metrics:
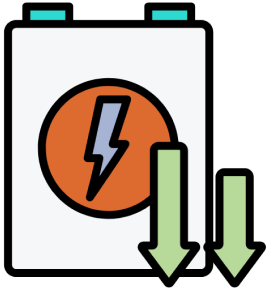
Lower Energy Consumption
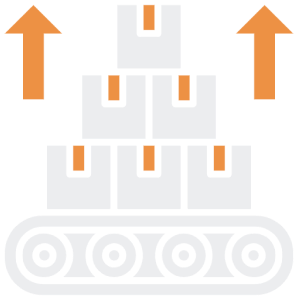
Optimize Productivity
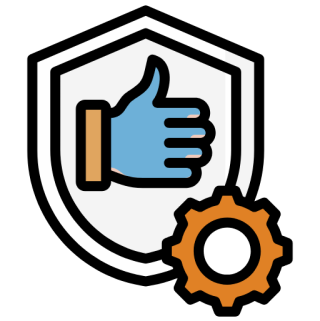
Improved Safety
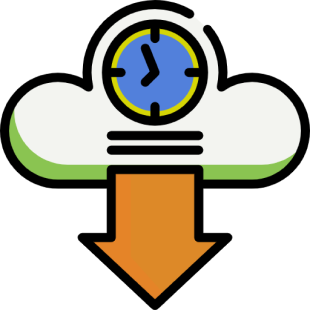
Reduced Downtime
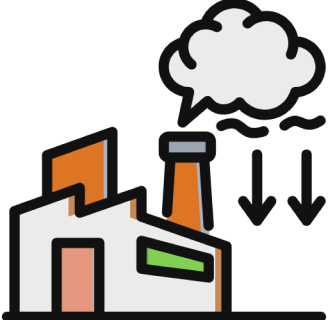
Lower Emissions
Combustion Systems Data
We analyze diverse data types to deliver actionable insights:
Operational Data
Furnace temperature, pressure, and burner power.
Energy Consumption Data
Fuel, oxygen, and air flow rates.
Safety & Reliability Data
Shutoff valves, pressure/temperature switches, UV sensors.
Emission Data
NOx, O₂, and CO sensor readings.
Ecosystem Data
Operating manuals, specifications, troubleshooting guides, and more.
Energy Efficiency
Identify and rectify operational inefficiencies and maintenance errors.
Production Optimization
Reduce CO₂ and NOx emissions through precise energy management.
Safety Enhancements
Predict and prevent device failures while ensuring regulatory compliance.
Minimized Downtime
Eliminate bottlenecks and boost operational continuity.
Sustainability Goals
Achieve precise control over emissions for greener operations.
How It Works
Our platform integrates seamlessly into your operations, delivering real-time insights and automation to enhance performance and efficiency.
Lower Energy Consumption
Ensure the reliability of safety devices and prevent errors for seamless operations.
Higher Production
Optimize burner management to reduce emissions and unplanned shutdowns.
Safety Improvements
Predict failures and maintain compliance with emission permits.
Reduced Downtime
Streamline processes to maximize yield and eliminate production bottlenecks.
Lower Emissions
Improve flow control and pressure measurement for sustainable performance.
Our AI Platform
Features and Capabilities
At Pyretek, we deliver cutting-edge AI solutions tailored for burner systems. Our platform seamlessly integrates with your sensors and controls to provide comprehensive, real-time insights into your furnace operations. Through advanced analytics, predictive AI/ML models, and actionable recommendations with Generative AI, Pyretek ensures optimized performance, safety, and sustainability.
Enhanced Monitoring
Cloud dashboards offering real-time visibility into burner systems with detailed metrics, trends, and AI-driven notifications.
AI-Powered Insights
Proprietary Machine Learning (ML) models for anomaly detection, event analysis, operational efficiency, and safety improvements.
Personalized Solutions
Targeted remediation, issue triage, and personalized recommendations for individual devices and entire fleets.
Generative AI Tools
Intuitive guidance for troubleshooting, system recommendations, and step-by-step action plans within your burner ecosystem.
THEY TRUST US
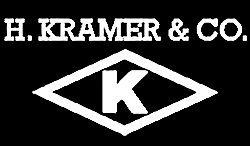
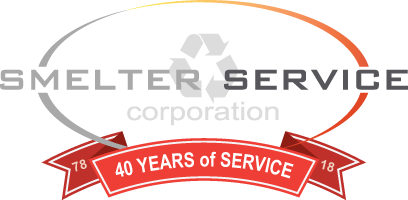
Use Cases
Explore how Pyretek optimizes combustion processes across various industrial applications
FREQUENTLY ASKED QUESTIONS
All You Need to Know